Warehouse meaning in English
A warehouse is a large building where goods and products are stored before they are sold or distributed to stores, businesses, or customers. It’s like a big storage space where items are kept until they are needed or ready to be shipped to their final destination.
Example:
The farmers stored their harvested crops in the warehouse.
Warehouse meaning in Tamil
Translation: கிடங்கு
கிடங்கு (Warehouse) என்பது ஒரு பெரிய கட்டிடம் ஆகும். கடைகள், வணிகங்கள் அல்லது வாடிக்கையாளர்களுக்கு பொருட்கள் விற்கப்படுவதற்கு முன் இங்கு சேமித்து வைக்கப்படும். இது ஒரு பெரிய சேமிப்பிடம் போன்றது, அங்கு பொருட்கள் தேவைப்படும் வரை அல்லது அவற்றின் இறுதி இலக்குக்கு அனுப்பப்படும் வரை சேமித்து வைக்கப்படுகின்றது.
Example:
The farmers stored their harvested crops in the warehouse.
விவசாயிகள் அறுவடை செய்த பயிர்களை கிடங்கில் சேமித்து வைத்தனர்.
Warehouse meaning Hindi
Translation: गोदाम
गोदाम (Warehouse) एक बड़ी इमारत है जहां सामान और उत्पादों को स्टोर, व्यवसायों या ग्राहकों को बेचने या वितरित करने से पहले संग्रहीत किया जाता है। यह एक बड़े भंडारण स्थान की तरह है जहां वस्तुओं को तब तक रखा जाता है जब तक कि उनकी आवश्यकता न हो या वे अपने अंतिम गंतव्य तक भेजे जाने के लिए तैयार न हो जाएं।
Example:
The farmers stored their harvested crops in the warehouse.
किसानों ने अपनी कटी हुई फसल को गोदाम में रख दिया।
Warehouse meaning in Malayalam
Translation: സംഭരണശാല
ചരക്കുകളും ഉൽപ്പന്നങ്ങളും സ്റ്റോറുകൾക്കോ ബിസിനസ്സുകൾക്കോ ഉപഭോക്താക്കൾക്കോ വിൽക്കുകയോ വിതരണം ചെയ്യുകയോ ചെയ്യുന്നതിനുമുമ്പ് സൂക്ഷിക്കുന്ന ഒരു വലിയ കെട്ടിടമാണ് സംഭരണശാല (Warehouse). സാധനങ്ങൾ ആവശ്യമുള്ളത് വരെ അല്ലെങ്കിൽ അവയുടെ അന്തിമ ലക്ഷ്യസ്ഥാനത്തേക്ക് ഷിപ്പ് ചെയ്യാൻ തയ്യാറാകുന്നത് വരെ സൂക്ഷിക്കുന്ന ഒരു വലിയ സംഭരണ ഇടം പോലെയാണിത്.
Example:
The farmers stored the harvested crops in the warehouse.
കർഷകർ വിളവെടുത്ത വിളകൾ സംഭരണശാലയിൽ സൂക്ഷിച്ചു.
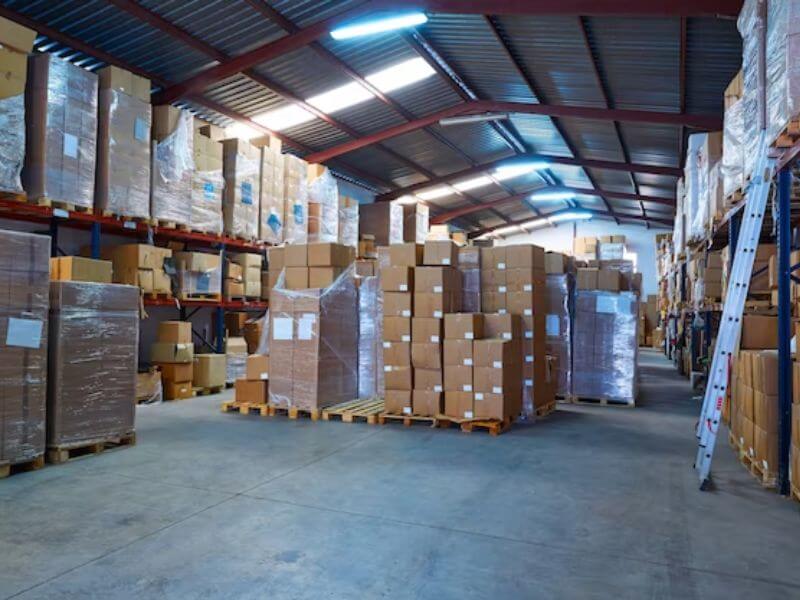
Elements of a Warehouse
Location:
The strategic placement of a warehouse is critical, considering factors such as proximity to suppliers, transportation infrastructure, and target markets. The location impacts accessibility and delivery timelines.
Infrastructure:
A warehouse consists of various physical components, including the building structure, storage systems, shelving, racks, pallets, bins, and equipment such as forklifts, conveyors, and automated systems. These elements enable efficient storage and handling of goods.
Layout:
The layout of a warehouse determines the flow of materials and the organization of different functional areas. It includes zones for receiving, storage, order picking, packing, shipping, and administrative tasks. The layout should optimize space utilization and streamline operations.
Inventory Management:
Effective inventory management is crucial in a warehouse. This includes accurately tracking stock levels, implementing inventory control measures, conducting regular audits, and utilizing inventory management software to optimize stock levels and minimize stock outs or overstocks.
Delve deeper into the topic of Inventory, and be a step ahead.
Safety and Security:
Safety is paramount in a warehouse environment. Safety measures include implementing proper storage practices, providing adequate lighting, maintaining clear signage, ensuring proper ventilation, and conducting regular safety training for employees. Security measures may include access control systems, CCTV cameras, and theft prevention measures.
Warehouse Processes
Receiving:
This process involves the acceptance and verification of incoming shipments. It includes checking quantities, inspecting for damages, recording product details, and updating inventory systems. Receiving may also involve quality control checks and storing goods in designated areas.
Put-away:
Once received, goods need to be organized and placed in appropriate storage locations within the warehouse. This process involves determining the optimal storage location based on factors such as item characteristics, demand patterns, and accessibility. Efficient put-away ensures easy retrieval and minimizes errors during order fulfillment.
Order Picking:
Order picking is the process of selecting and collecting items from the warehouse to fulfill customer orders. It involves identifying the location of the items, retrieving them from storage, and assembling them for packaging. Optimization techniques, such as batch picking or zone picking, can be employed to enhance efficiency.
Packing:
The packing process involves preparing items for shipment. It includes selecting appropriate packaging materials, labeling packages with shipping information, and ensuring items are securely packaged to prevent damage during transit. Efficient packing can help reduce shipping costs and minimize product damage.
Shipping:
The shipping process involves preparing shipments for transportation. It includes coordinating with carriers, generating shipping documents (such as bills of lading or customs documentation), loading goods onto vehicles, and tracking shipments until they reach their destination. Efficient shipping processes help ensure timely delivery.
Returns Management:
Managing product returns is an essential warehouse process. It involves receiving returned items, inspecting them for damage or quality issues, updating inventory systems, and determining the appropriate action (e.g., restocking, repair, or disposal). Effective return management contributes to customer satisfaction and inventory accuracy.
Inventory Control:
Inventory control processes involve ongoing monitoring, tracking, and analysis of inventory levels. This includes conducting regular stock counts, reconciling discrepancies, identifying slow-moving or obsolete stock, and implementing measures to optimize stock turnover and minimize carrying costs.
By integrating these elements and processes effectively, warehouses can operate efficiently, maintain accurate inventory, and facilitate the smooth flow of goods throughout the supply chain.
Example
Warehousing can be seen in a global e-commerce company that operates multiple warehouses strategically located near major cities. These warehouses serve as distribution centers where products from various suppliers are received, sorted, stored, and shipped to customers worldwide.
Upon receiving shipments, the warehouse staff carefully inspects and checks the quantities and quality of the products before recording them into the inventory management system. The goods are then put away in designated locations based on their characteristics and demand patterns, optimizing storage space and accessibility.
When customer orders are placed, the warehouse utilizes efficient order picking techniques, such as zone picking, to gather the items accurately and quickly. The selected items are then packed securely with appropriate packaging materials, labeled with shipping information, and prepared for shipment. The warehouse team coordinates with different carriers to ensure timely and cost-effective delivery.
Additionally, the warehouse implements robust inventory control measures, regularly conducting stock counts, reconciling discrepancies, and analyzing inventory data to optimize stock levels and minimize carrying costs. This example showcases the essential elements and processes involved in a modern warehousing operation, facilitating the efficient movement of goods from suppliers to end customers.
FAQs:
- How can warehouses optimize space utilization?
Warehouses can optimize space utilization by implementing efficient storage systems such as pallet racking, mezzanine floors, and vertical storage, and by utilizing inventory management software to track and manage inventory levels accurately.
- What measures can warehouses take to enhance safety?
Warehouses can enhance safety by implementing proper storage practices, maintaining clear signage, conducting regular safety training for employees, and implementing safety protocols such as wearing personal protective equipment (PPE) and enforcing strict adherence to safety guidelines.
- How can warehouses improve order picking efficiency?
Warehouses can improve order picking efficiency by implementing technologies like barcode scanning and voice picking, organizing the layout to minimize travel distances, utilizing efficient picking strategies like batch picking or zone picking, and employing trained staff and streamlined processes to minimize errors and delays.