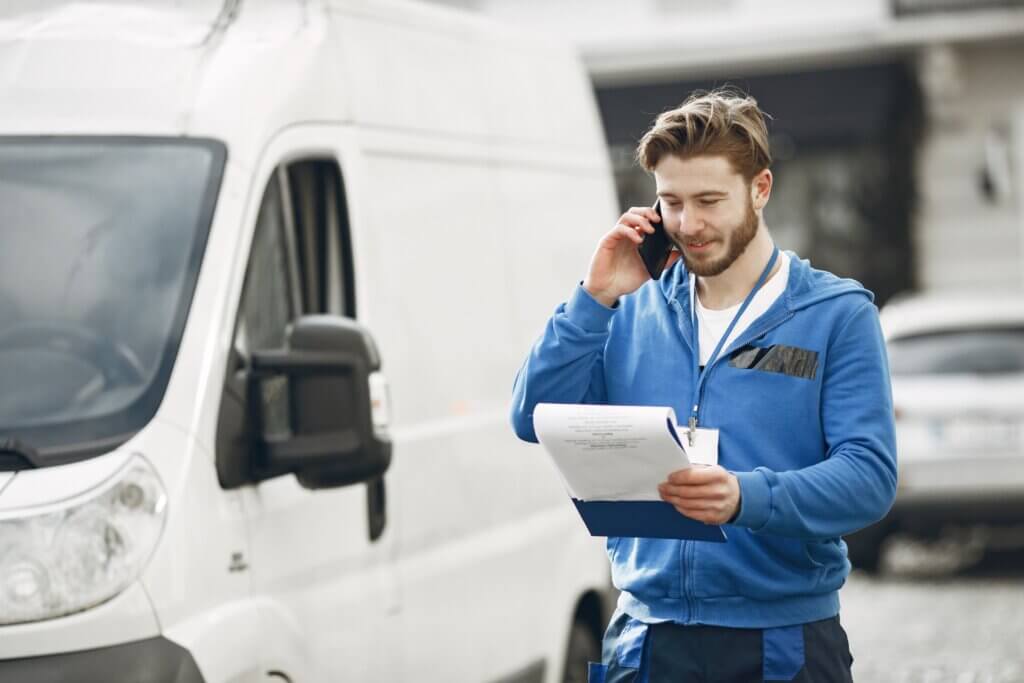
Just-in-Time (JIT) is a production and inventory management system that aims to produce and deliver goods or services precisely when they are needed, neither too early nor too late. It is a lean manufacturing strategy that focuses on reducing waste and improving efficiency in the production process.
Benefits of Just-in-Time (JIT)
Cost Reduction:
JIT minimizes inventory carrying costs, including storage, insurance, and depreciation, by reducing inventory levels. It eliminates the need for excessive stockpiling, allowing companies to invest their capital in other areas of the business.
Waste Reduction:
JIT eliminates waste associated with excess inventory, such as obsolescence, spoilage, and damage, by producing goods only when needed. It also identifies and eliminates bottlenecks, defects, and non-value-added activities, reducing waste in the production process.
Improved Efficiency:
JIT promotes smooth and continuous production flow, increasing productivity and reducing downtime. It follows a pull-based system triggered by customer demand, ensuring efficient and effective allocation of resources.
Quality Enhancement:
JIT emphasizes quality control and defect prevention. With reduced inventory levels, defects are more likely to be identified and rectified before they escalate. Additionally, JIT encourages close collaboration with suppliers to ensure the delivery of high-quality materials.
Flexibility and Responsiveness:
JIT enables quick responses to changes in customer demand and market conditions. By maintaining minimal inventory levels, businesses can easily adjust their production to match fluctuating demand patterns, reducing the risks of overproduction or stock outs.
How Just-in-Time Works?
Demand-driven Production:
JIT operates on a pull-based system, where production is driven by actual customer demand rather than forecasts or speculative inventory buildup. This approach minimizes the risk of overproduction and ensures that goods are produced only when needed.
Synchronized Workflow:
JIT emphasizes a smooth and synchronized flow of materials, information, and activities throughout the production process. Each stage of the process is coordinated to minimize delays, waiting times, and bottlenecks, resulting in a streamlined and efficient workflow.
Continuous Improvement:
JIT encourages a culture of continuous improvement and waste elimination. Companies regularly review and refine their production processes, seeking ways to reduce setup times, eliminate defects, improve efficiency, and optimize resource allocation.
Close Supplier Collaboration:
JIT relies on close collaboration and partnerships with suppliers. Suppliers deliver materials and components in small, frequent batches, timed to align with production requirements. This reduces inventory holding costs and ensures a steady supply of inputs.
Kanban System:
The Kanban system, a visual signaling method, is often employed in JIT. It uses cards or other visual cues to signal the need for more materials or products at various stages of the production process. This helps maintain a smooth flow of materials and prevents stockouts or overstocking.
Overall, Just-in-Time aims to achieve optimal production efficiency by reducing waste, eliminating excess inventory, and aligning production with actual demand. It is a holistic approach that requires effective coordination, continuous improvement, and strong supplier relationships to achieve its full benefits.
Example:
One common example of Just-in-Time (JIT) implementation is in the automotive industry. An automobile manufacturer adopts JIT principles to minimize inventory and improve efficiency.
Instead of stockpiling large quantities of components and parts, the manufacturer collaborates closely with suppliers to ensure timely delivery of the necessary parts in small batches, precisely when they are needed on the assembly line. This allows for streamlined production processes, reduced storage costs, and faster response to changing customer demands.
By implementing JIT, the manufacturer achieves a more efficient workflow, eliminates waste associated with excess inventory, and maintains flexibility to meet customer requirements promptly.
FAQs:
- What are the potential risks of implementing Just-in-Time (JIT) in a production system?
The main risks include supply chain disruptions, increased vulnerability to supplier issues, and potential production delays if parts or materials are not delivered on time.
- How does JIT impact inventory management?
JIT reduces inventory levels by emphasizing a pull-based system, where production is driven by customer demand, leading to lower storage costs and minimized waste associated with excess inventory.
- Can JIT be applied to service industries as well?
Yes, JIT principles can be applied to service industries, such as healthcare or hospitality, by focusing on minimizing waiting times, optimizing resource allocation, and delivering services on-demand to enhance efficiency.